Bentley Speed 6: A Tail Of Two Bodies.
Article and images by Max Houston, Janurary 2017.
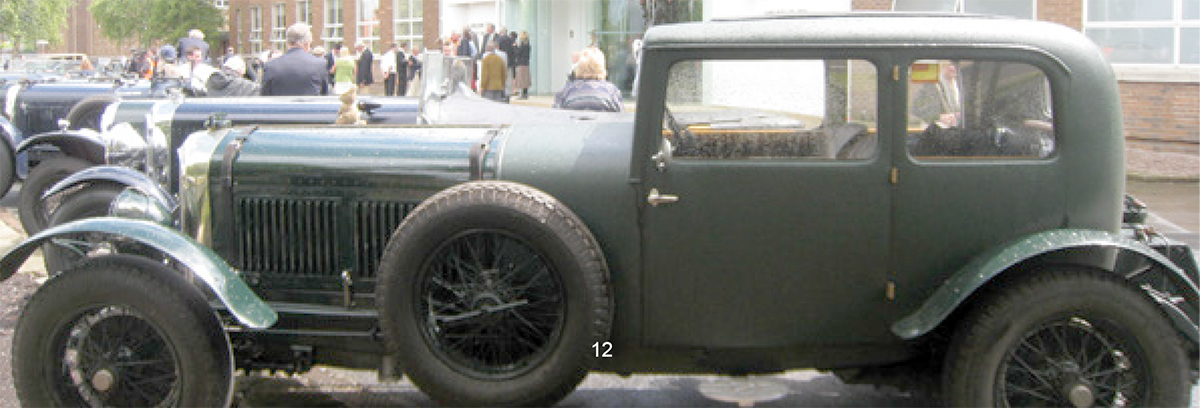
The Speed 6 in front of the Bentley Factory at Derby, 2011 Britain by Bentley Tour.
Around 30 years ago, I bought a Bentley Speed 6 from England, fully dismantled with many parts missing, broken or otherwise damaged. There was of course no body or any related fittings
The chassis had been shortened, there were no front brake drums and the front brake plates and mechanisms were unusable. It therefore made sense to build the almost mandatory Le Mans Replica.
On reading and learning Bentley lore I realised that this car had started life beside the most famous Bentley of all, known as ‘Old Number 1’. The engine and chassis numbers of my car were two cars prior to that famous car, the first 6-cylinder racing car and the car that won at Le Mans in 1929 bearing the race number 1. It won again in 1930 when its race number was 4, but it was always known as Old Number 1 from the previous year.
The 6-cylinder racing cars had the self-wrapping brakes, from the current 4.5 litre 4-cylinder cars. All other 6-cylinder cars had the brakes standard on all Bentleys, but with a push-on operation and a vacuum booster. The self-wrapping brakes were not great, but with very thick and soft lining, and with a large range of adjustment accessible from the driver’s seat, were used. One report I read about these brakes during Le Mans racing said, “by the 20th hour the brakes were gone”. We therefore added, for the BBB tour, a Clayton Dewandre vacuum hydraulic booster from a post-war Commer truck, converted for mechanical operation to operate the self-wrapping brakes; What a transformation this made! Finally, brakes to match the performance.
Some years and much work later the Speed 6 was Outright Winner in the BDC (NSW) Concours in 1995 and Runner-Up in 1996. The Le Mans body has no side curtains, a rather skimpy hood, low sides, and is not much fun in bad weather.
While in New Zealand during 2004, we became aware of the advantages of an open car. We saw much more of the magnificent scenery than the unfortunates in the closed cars, allowing us to see the best that New Zealand had to offer.
When we decided to go to the UK for the 75th Anniversary BDC Tour of Britain, the decision was made that the car should have a body more suited to the unpredictable weather conditions there.
In about 4 hours, the Le Mans body came off the chassis, and we set about designing and building a new closed 2-door body. Criteria was that the body needed to fit between the rear guards, and could be easily swapped for the other body if or when required.
To achieve these criteria, the dashboard wiring was modified to incorporate two large trailer type plugs and sockets (the dash and instruments were mounted from outrigger brackets) had to be removable so the body could be lifted out and then replaced with another body.
Since this time, I haven't yet seen the need to change the body back, but I estimate that should two enthusiastic people want to change it back, they could accomplish it in a day, given some suitable lifting tackle.
The intention was to provide maximum visibility from the Coupe body so that the tallest Castle or mountain range could be seen or photographed with ease. To enable this, we persuaded the people at Webasto Sunroof people to assist, who provided a complete assembly including folding fabric sunroof with electric flexible rack and pinion operation. The new body was built to incorporate this.
The body was framed in Australian silky oak, a very strong, close-grained but lightweight timber. As well as being one of the timbers used in the now-defunct Australian coachbuilding industry (except for vintage car restorations and repairs in shops such as our VMG), it was used for high quality furniture in the ‘between the wars’ period in Australia (as oppose timbers from Indonesia and Malaysia). Owing to the shortened wheelbase of the Le mans car (11’ 2”), the rear-seat compartment is now a little cuddlier.
The Coupe body as previously mentioned needed to fit between the rear guards and clear the large fuel tank behind. The same rear profile of the LM body was reproduced and extended to meet the curved roof line which gave it a rather cute backside. Steel bracing was fabricated to prevent movement in the main joints with the associated creaking common in wood-framed saloon bodies of the era. For safety reasons, such as in a side collision, the whole body was panelled in 16-gauge aluminium instead of just panelling the compound curves as was done in the real fabric bodies (no side air bags or even running boards and valances to protect in the event of a side-impact accident)
The same green Everflex material (a modern version of the vintage fabric) as on the LM body was stretched over the panels with a minimum of sown seams. On tour, it proved to be draught. Leak and rattle free, with no wind noise at all speeds up to about 80 mp/h (approx. 130 km/h). As the Le Mans handbrake lever is positioned outside the body, a new lever was made to fit the same mounting bracket and ratchet, and fit inside the front door pillar.
The racing seats as originally fitted were far too spartan for a more comfortable closed body vehicle, so new bigger folding ones were made and the whole interior was trimmed in brown boot leather Connolly hide, while the grey felt hood lining matched the lining of the folding roof perfectly. Windscreen and door capping’s were made from the same oak as the body, lacquered and polished. Two larger ‘B’ step plates were fitted without drilling the chassis, to provide easier access for front and rear passengers.
New side and blinker lights were fitted, inboard of the front guards, as the Le Mans cars had lights in a rather vulnerable position on the scuttle at the back of the bonnet.
After the car returns home, and when time permits, it will probably acquire a trunk which will cover the large fuel tank, making a well-proportioned and more practical car.
The Bentley was shipped on 15th April, and I arrived in London on 2nd June.